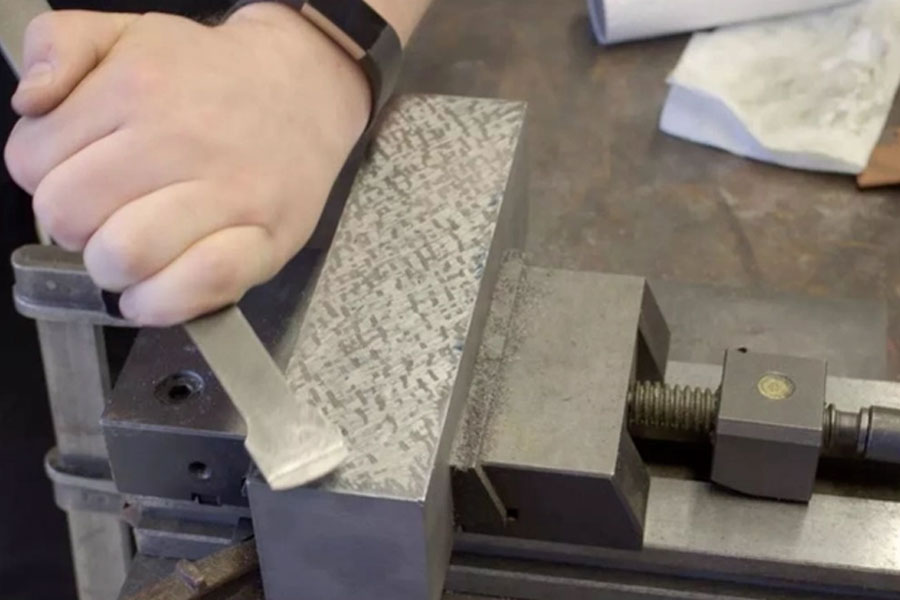
Swiss machine tools in the end how strong, why the accuracy of machine tools can do the world’s first-class, when it comes to machine tools, the first thing that comes to mind is the accuracy of the machine tool, usually represents the maximum accuracy of the parts that can be processed by the machine tool, we all know that the machining accuracy of machine tools will only lose and not increase, for example: 0.01 mm accuracy of the machine tool can only be processed with an error greater than 0.01 mm workpiece, in such a In this case, in order to create a high-precision machine tool, we need to use a higher precision machine tool to process, then a higher level of machine tool is how to be manufactured?
When it comes to high-precision machine tools, many people think of Germany and Switzerland, the Swiss machine tools in the end how powerful it is, for a long time, the Swiss machine tool exports ranked in the world’s top five, Swiss machine tools in the past 30 years has maintained a steady record of the world’s first, more than 150 countries are customers of Swiss machine tools, especially precision machine tools, very popular with countries around the world, Switzerland as one of the German-speaking countries, has been As one of the German-speaking countries, Switzerland has inherited the “craftsmanship” of the German-speaking countries, and has a dedication to excellence in craftsmanship.
Once a Swiss boss to show the machine tool drawings to everyone, but no one dares to imitate, because the key components, processes, spare parts are all purely handmade, some people may have questions, not a machine tool, why not use machine tool processing?
You know that through the machine tool to manufacture machine tools, precision is certainly no way to exceed the original machine tool, leaving aside the human factor, only rely on machine tools to create a ten-micron machine tool, you must use 1 micron or higher machine tools to do, so through the assembly line processing out of the machine tool, the accuracy is certainly not high, the real high precision machine tools are polished by hand little by little, for example: the United States Space telescope is polished by hand, the lens of the lithography machine is also polished by hand.
The most expensive Rolls-Royce in the world is also made by hand. According to the relevant data, each Rolls-Royce car is carefully polished by 60 hands before it leaves the factory, and it is only sent to consumers after 450 hours of continuous debugging by craftsmen. And high-precision machine tools are also built on the original machine tools, after the manual hands and eyes repeatedly grinding ratio, and finally formed a standard system, through a new standard elimination of an old standard process, which is why we can always see the Swiss factory technicians with a knife in which side scraping frustration, if you look purely at the appearance of these workpieces, you certainly If you look at the appearance of these workpieces, you can’t see anything. Usually the technician will apply the coloring agent to the machine parts and put them on the plane of the tool, so that the areas that need to be scraped off will be revealed, and keep repeating this action, the surface of the workpiece will be closer and closer to the standard jig, and finally the workpiece can be reproduced perfectly as the standard jig.
Usually these workpieces are first milled to a size close to the range of a few thousandths, sent to heat treatment to release the residual pressure, and then sent to the hands of the technician for grinding, although grinding takes a lot of time, but grinding can replace the cost of high precision machine tool manufacturing, more importantly, when the workpiece requirements are very high, even high precision machine tool processing should take into account the human factors, such as Large bed castings, usually requires a series of heavy pressure operations, in the case of precision to one thousandth, due to the release of clamping force, will cause the workpiece to deform, thus affecting the accuracy of the workpiece, the heat generated by the workpiece during processing will also cause the workpiece to distort, the
This is when manual grinding can replace the machine tool can not complete the task, this is also the biggest advantage of manual grinding, manual without any clamping force, more will not produce heat, so generally pure hand-built workpiece are much higher than the precision of machine processing, for example: we do not have CNC machine tools in the early days, to process the propeller of the submarine can not be processed out of the perfect Archimedes screw line, how to do? All rely on workers to polish out by hand, by imitating the line of machine tools, so that high-end machine tools often require the most primitive manufacturing methods, which is one of the fundamental reasons why the Swiss machine tools from the machine tool processing, choose to build purely by hand.
In general, the Swiss machine tools are so successful because of the Swiss craftsmanship, from small watches to large machine tools need to be finely honed, which has trained a number of technicians, and it is with these people, Switzerland has Mikron, Starrag, Tonus and other well-known brands. Although Switzerland is a small country, the lack of natural resources, but Switzerland is the most developed country in the world, they rely on their own hands to infinitely improve the precision, and then sell precision machine tools to the world, I believe that in the future machine tool industry precision upgrade, we can also use their own hands to create more miracles.